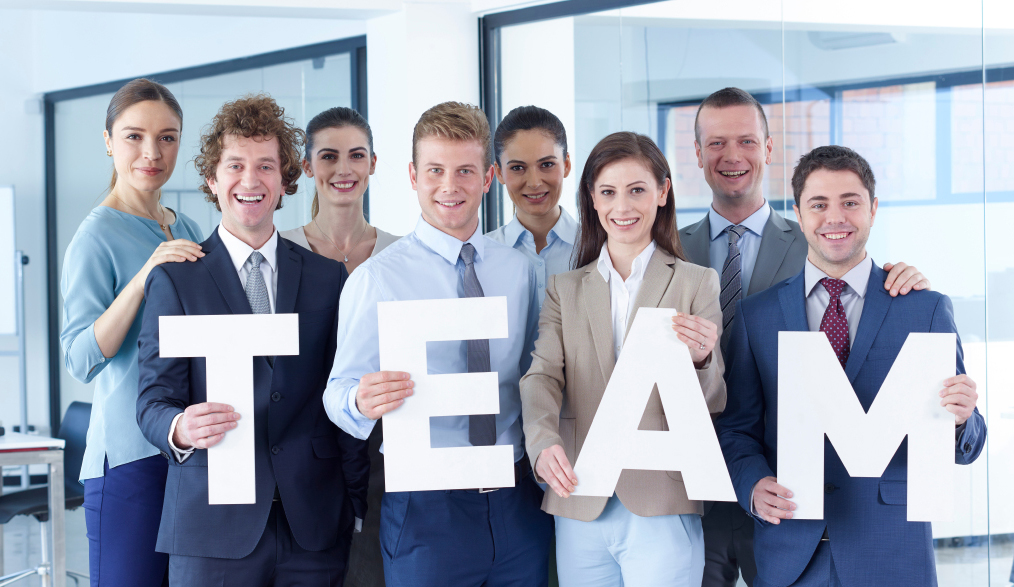
OUR TEAM
TT Motor has experienced reduction motor R & D team, brushless motor R & D team and hollow cup motor R & D engineer team, extensive use of FMEA, VE, CAD and other advanced design technology as well as MEA motor performance analysis system, starting torque tester, gear box design software and other latest analysis system to design products.
TT Motor has experienced reduction motor R & D team, brushless motor R & D team and hollow cup motor R & D engineer team, extensive use of FMEA, VE, CAD and other advanced design technology as well as MEA motor performance analysis system, starting torque tester, gear box design software and other latest analysis system to design products.
Different from the traditional plastic mold design, the tooth thickness, modulus and pressure Angle of the micro gear need to be modified with empirical data, and can not be directly processed according to the shrinkage rate. Our experienced engineers make extensive use of the cavity parametric calculation software of the plastic gear mold to directly generate the gear contour, which is used to modify the gear shape and improve the precision of the tooth shape. The tooth profile generated by the software can be used in line cutting machine and discharge machining to improve the machining accuracy of die.
With rich experience in R&D and production, we have a first-class technical and management team and passed ISO9001 quality system certification. Over the years we are committed to motor technology and production process innovation, and has obtained a number of national patents, especially in the hollow cup motor high voltage drive research has industry advantages. Professional R & D and production of high-performance hollow cup motor and brushless motor manufacturers, starting from the details, based on the design, to highlight the product characteristics, reliable product quality performance. Every motor or driver is strictly tested out of the factory, and every motor or driver is strictly tested out of the factory.